(报告出品方/作者:华泰证券,肖群稀,关东奇来,时彧)
1 “十四五”构建“大氢能”图景,燃料电池先行
氢能是国家能源安全,节能减排的优选方案
氢能将成为能源安全的重要组成部分。预测2030 年中国氢气需求量 3715 万吨,在终端能源消费中占比约为 5%; 2060 年 13030 万吨,在终端能源消费中占比约为 22%。国际能源署预测,到2070 年 全球对氢气的需求将达到 5.2 亿吨。世界能源理事会预计,到2050年氢能在全球终端能源消费量占比 25%。
2021 年,全球主要国家共销售氢车 16,313 台,同比增长 68%,韩国占据总销量的 52%。 受强势补贴政策驱动,韩国市场延续了 2020 年的增长势头,全年共售出 8,498 台氢车, 约占全球总销量的一半。美国全年氢车销量为 3,341 台,较 2020 年激增 2.5 倍,主要原 因是 2020年疫情导致销量基数过低;日本全年共售出氢车 2,464 台,同比增长 67%,主 要受益于 2020 年底新一代丰田 Mirai 的上市。德国共售出氢车 424 台,同比增长 38%。 中国全年氢车销量为 1,586 台,同比增长 35%。全球主要国家氢车保有量为 49,562 台, 同比增长 49%。
相同里程下一辆重卡的二氧化碳排放量约为一辆乘用车的十倍,氢能物流车/乘用车/重卡 预计单车年碳减排量达 9.8t/2.1t/187.6t,提高重卡的新能源转化率是商用车发展的重头戏。 重卡作为物流运输的主力生产工具,单车运营里程长、运营次数多、柴油消耗总量高,成 为氮氧化物、一氧化碳和颗粒物等污染物的主要排放来源,造成严重的环境污染。根据商用汽车的统计,2021年我国重卡保有量约有 850 万辆,重卡的污染排放量占到商用车总排放量的近 6 成。
示范城市群探索多元应用场景,政策精准补贴
“3+2”示范城市群格局形成,探索多元应用场景,交通领域是氢能产业应用的先导部分。 2021 年 9 月,我国首批三个燃料电池汽车示范城市群落地,分别由北京市、上海市和广 东省佛山市牵头。2021 年 12 月 28日,河南、河北两大燃料电池汽车示范城市群正式启 动。全国“3+2”燃料电池汽车示范格局形成,合计共 47 座城市。国家发改委能源研究所 环境中心主任熊华文提出:“交通领域是氢能产业应用的先导部分,十四五期间,氢能将探 索走多元化的应用之路,在工业、建筑等领域进行探索,构建“大氢能”图景。
国补补贴采取“以奖代补”方式精准补贴,按照示范城市群任务目标完成情况给予奖励。 示范城市群奖励为期 4 年,各年度奖励比例为 20 年/21 年/22 年/23 年:1.3/1.2/1.1/0.9, 可近似看作 21 年、22年奖励在前一年基础上退坡 10%,23 年奖励退坡 20%。财政部分别在燃料电池汽车推广应用和氢能供应两个领域给予示范城市群补贴,原则上 1 积分约奖 励 10 万元。示范期间将根据示范进展情况适度调整补贴标准和技术要求。积分上限分别 为 15000 积分和 2000 积分,即补贴金额上限为 15 亿元和 2 亿元。为推进产业合理布局, 示范区以外的地方原则上不宜再对燃料电池汽车推广给予购置补贴。
示范城市群中上海补贴政策已经落地,其余示范城市群政策有望逐步落地。上海的补贴力 度较大:1)与国补进行 1:1 配套,每 1 积分国补+地补共 20 万元的奖励,由统筹资金安 排 15 万元,燃料电池系统生产企业所在区安排 5 万元;2)补贴范围涵盖了制储运加用全 产业链各个环节,将整车企业运营纳入补贴,将核心零部件从国补的 8 大扩展到 9 大,增 加了储氢瓶阀;对加氢站建设和氢气零售价给予补贴。
补贴政策鼓励续航里程高、功率大的商用车型,以上海地区 31 吨以上重卡车型为例,国 补+地补超过 100 万,补贴后车辆购置成本与燃油车持平。根据最新积分奖励政策,针对 功率大于 75kW 的燃料电池车,给予更高的积分和补贴支持。纳入奖励车辆的纯氢续驶里 程应不低于 300km,对于 31 吨以上的重型货车以及矿山、机场等场内运输车辆,续驶里 程可放宽至 200km。这有利于诸如矿用卡车、机场摆渡车等场内运输车型应用。车型上, 轻中型货车(<12 吨)和中小型客车(<10m)奖励金额最低,大型客车和重型货车补贴 力度更高,在重型货车中,12-25 吨、25-31 吨和 31 吨以上 3 档,各档奖励金额呈阶梯式 上升。根据香橙会研究院,目前 31 吨氢能重卡售价为 150 万左右,补贴超过 100 万,补 贴后购置成本与一辆相近规格的柴油重卡拖车已大体持平。
氢能车进入规模示范阶段,2025 年保有量有望达到 10 万辆
25 年 10 万辆,30 年 100 万辆的目标有望实现。中国氢能联盟预测 2025 年中国氢燃料电 池汽车保有量 10 万辆,2030 年保有量 100 万辆,截至 2021 年,国内燃料电池汽车保有 量为 8938 辆,2022-2025 年 CAGR=83.1%,2026-2030 年 CAGR=48.5%,根据复合增 速,我们预计 2025 年中国燃料电池汽车销量为 4.6 万辆,2030 年为 37 万辆。根据示范 城市群的示范目标,2025 年合计为 3.3 万辆,考虑其他非示范氢能规划持续落地,我们预 计 2025 年中国氢燃料电池汽车 10 万辆的保有量目标有望实现。
中汽协数据, 2016-2021 年国内氢燃料电池汽车销量分别为 629、1275、1527、2737、 1177、1586 辆,截至 2021 年,国内燃料电池汽车保有量为 8938 辆。 若氢燃料电池在商 用车全面推广,每年潜在市场空间超过 180 万辆/年。根据中汽协数据,2020 年国内重卡、 市政环卫车、公交车和大巴车销量分别为 162.3 万辆、6.9 万辆、6.6 万辆和 5 万辆,若氢 燃料电池车全面替代原有重卡、环卫、公交、大巴等燃油车,潜在市场需求合计 180.8 万 辆/年。
工信部推荐燃料电池车型数量持续增加, 推荐车型从客车转向重卡。根据工信部《新能源 汽车推广应用推荐车型目录》(2017-2021 年),2017-2021 年累计共推荐 760 款新能源汽 车,其中,2021 年共推荐车型 303 款,客车、重卡、环卫车和低温冷藏车推荐车型数量 占比分别为 33.0%、20.3%、21.2%和 12.7%,客车推荐车型占比 2019 年为 69%,2021 年出现较大下降,重卡占比大幅增加,推荐数量占比从 2019 年的 3%增长至 21 年的 20.3%。
2021 年氢能重卡销量 779 辆,同比增长 42 倍,占新能源重卡的份额从 2020 年的 0.7%上 升至 2021 年的 7.46%。2021 年,新能源重卡累计销售 10448 辆,同比增长 3 倍。新能源 重卡在重卡销量中的比重由年初的 0.09%上升至年末的 5.67%。燃料电池重卡 21 年销量 779 辆,同比增长 42.28 倍,在新能源重卡中的份额从 2020 年的 0.7%上升至 7.46%,成为 新能源重卡领域重要细分市场。
纯电动车的续航里程和补能时间仍不理想,长期看燃料电池更适合长途载重运输。纯电动 是新能源重卡中最为成熟的技术路线,较汽柴油重卡而言更加环保,可实现零排放。然而 由于技术局限,纯电动车的续航里程和补能时间仍不理想,即便采用换电模式减少充电时 间,也只能在换电站辐射的作业半径内进行运输工作,提升续航里程将面临载重量的降低。 这些因素都大大限制了电动重卡的适用场景,为氢燃料电池车的进入留下了空间。相较于 纯电,氢燃料电池有能量密度更高、自重低、加注快、耐低温等优点,这决定了氢燃料电 池车天然适用于固定路线、中长途干线和高载重的场景中。(报告来源:未来智库)
2 降本目标:补贴前全生命周期降本 46%可与电车平价
长途、大功率应用场景下,燃料电池系统优势明显
氢燃料电池车型更适用于路线相对固定、加氢便利等区域性应用场景。相比纯电动车型, 氢燃料电池车克服了能源补充时间长、低温环境适应性差的问题,提高了营运效率,与纯 电动车型应用场景形成互补;按照“氢电互补、宜氢则氢、宜电则电”的原则,同时结合各 场景的应用潜力,受制于当前储氢、加氢基础设施及燃料电池发动机水平不足以支持长途、 大功率需求场景,氢燃料电池车型更适用于路线相对固定、加氢便利等区域性应用场景, 主要有以下应用场景。
氢能在交通领域的应用将逐步向长续航、大载重的场景过渡。根据氢蓝时代常务副总裁曹 桂军在 2021 势银氢能与燃料电池产业年会上发表的《燃料电池系统开发与多场景应用》 的主题演讲,预计 2025 年燃料电池系统主要额定功率为 130~180kW,燃料电池系统最大 额定功率将大于 180kW,氢能在交通领域的应用将逐步向长续航、大载重的场景过渡。
经济性决定因素:购置成本、氢耗及氢气价格
燃料电池汽车成本包括车辆购置成本和使用成本,燃料电池汽车的燃料经济性决定了使用 成本,它与两个因素直接相关:百公里氢耗量和氢气价格。
《中国氢能产业发展报告 2020》对车用燃料电池系统提出的成本目标:
1) 系统成本:2025/2035/2050年商用车燃料电池系统成本目标为 3500/1000/ 500 元 /KW。以 2020 年为基数,2025/2050 年分别下降 30%/80%;
2) 系统功率:2025年燃料电池重卡、客车、物流车的系统功率分别为 150/100/55kW, 2050 年分别为 300/200 /100kW;
3) 百公里耗氢:2025 年燃料电池重卡、客车、物流车分别为 8.5 /5.5/2.5 kg/100km; 2050 年分别为 6/3.5 /1.5 kg/100km。以 2020 年为基数,氢耗 2025/2050 年分别下降 17~23%/45%~50%;
4) 氢气成本:2025 年为 20 元/ kg,2035 年为 10 元/ kg,以 2020 年为基数,氢耗 2025/2035 年分别下降 43%/71%。
2017 年发布的《节能与新能源汽车技术路线图》提出的降本要求更高:
1) 燃料电池系统:商用车燃料电池系统成本 2020/2025/2030 年分别为 5000/2000/600 元/kW,以 2020 年为基数,2025/2030 年分别下降 60%/88%;乘用车燃料电池系统 成本 2020/2025/2030 年分别为 1500 /800 /200 元/kW ,以 2020 年为基数, 2025/2030 年分别下降 46%/86.7%;
2) 储氢系统成本:2020/2025/2030 年分别为 3000//2000/1800 元/kg,以 2020 年为基数, 2025/2030 年分别下降 33%/40%。
以 18 吨重卡车型为例降本空间测算:燃料电池车 VS 柴油车 VS 纯电车 基于中国、美国和日本的成本预测数据,根据车用燃料电池系统动力匹配的特点,分析燃 料电池与纯电动卡车(18t)的成本差异。根据上海捷氢 2021 年 9 月发表的论文《基于 TCO 分析氢气价格对燃料电池重卡经济性的影响》,我们选取载重 18t 的一汽解放 J6L4×2 厢式运输车,车辆使用场景为车队营运重卡,该运输车需要满足日均 500km 以上的长途 运输需求,使用时间为 5 年完成 100 万公里。结论如下:
1) 购置成本:燃油重卡价格约 20 万,补贴前纯电重卡约 71.6 万,补贴后为 67.6 万,补 贴前燃料电池重卡约 96.9 万,补贴后为 16.8 万。补贴前氢能车的购置成本分别高过 燃油重卡 80%,高于纯电重卡 35%。
2) 运营成本:燃油重卡柴油费用为 1.61 元/公里,电动车电费为 0.88 元/公里,补贴前燃 料电池重卡能源使用成本为 2.01 元/公里,补贴后燃料电池重卡氢气费用为 1.58 元/公 里,低于柴油重卡的运营成本。 补贴后氢能车的燃料成本低于燃油重卡,高于纯电重 卡 80%。
3) 全生命周期成本来看,补贴前,燃料电池重卡全生命周期成本高出燃油重卡 36%,高 出纯电重卡 46%。补贴后,燃料电池汽车全生命周期的成本与低于柴油重卡,略高于 纯电重卡 7%。
如果 2025 年和 2030 年氢燃料电池汽车性能及成本的达到《节能与新能源汽车技术路线图》 规划目标,则 18 吨重卡全生命周期成本 2025 年为 255.86 万,2030 年为 179.71 万,分 别比 2021 年燃油重卡成本低 22.79%和 45%,比 2021 年纯电动重卡低 5%和 31%。
需要注意的是:类似车型的情况下,燃料电池汽车的续驶里程主要取决于氢系统的储氢量, 纯电动汽车的续驶里程主要取决于电池的容量,锂电池应用于重型车辆时,锂电池的自重 不可忽略,根据高工锂电的数据,我们以一辆续航里程 200 公里的 30 吨纯电动卡车为例, 锂离子电池容量约为 400kWh,使用 300Wh/kg 的锂离子电池,电池自重高达 1.3 吨,如 果续驶里程提高到 800-1000 公里,电池自重将高达 6 吨以上;而 30 吨的燃料电池卡车百 公里氢耗约为 10kg,使用储氢密度在 5.7%的 70MPa 储氢系统,续驶里程为 1000 公里时 燃料电池系统与储氢系统重量的总和仅 2 吨左右。
降本路径:国产化推动规模化
目标:2025 年掌握关键技术,2030 年完全实现关键技术的自主可控 根据《节能与新能源汽车技术路线图 2.0》发展目标:到 2025 年,基本掌握关键技术,实 现 PEMFC 电动汽车规模化推广应用,建设 1~100kW 级 PEMFC 分布式发电示范项目; 到 2030 年完全掌握核心关键技术,建立完备的产业链,实现大规模推广应用;到 2050 年 实现普及应用。
质子交换膜燃料电池(PEMFC)是现阶段国内外主流应用技术。燃料电池通过电化学反 应直接发电,不受卡诺循环限制,没有机械传动损失,理论发电效率远高于内燃机。质子 交换膜燃料电池凭借启动时间短、操作温度低、结构紧凑、功率密度高的优点成为燃料电 池汽车迈入商业化进程的首选。
我国已经初步实现了 PEMFC 全产业链的国产化,逐步发展到产业规模持续扩张、基础设 施逐步完善的产业化初期阶段。2017 年以来,国内燃料电池系统核心技术取得显著进步, 初步掌握了整车、动力系统与关键部件的关键技术,基本建立了具有自主知识产权的燃料 电池轿车与燃料电池城市客车动力系统技术平台,实现了百辆级动力系统与整车的生产能 力。我国燃料电池汽车行业已基本形成以整车制造及燃料电池系统为牵引的燃料电池汽车 供应链和产业链体系,产业链覆盖燃料电池汽车整车、燃料电池系统及零部件,以及加氢、 制氢、储氢等环节。
我国领先企业的电堆技术参数已经和国际先进企业接近。以巴拉德、本田、丰田为首的国 际先进企业最大功率在 130~140kW,我国清能股份的 VLS II Pro 电堆的最大功率可以达 到 165kW,根据清能股份总经理张弛在 2021 势银氢能与燃料电池产业年会上发表的题为 《大功率燃料电池电堆的商业化》的主题演讲,清能股份已经在 2021 年实现了 170kW 电 堆的批量化应用,预计将在 2022 年一季度推出 250kW 电堆,截至 2021 年底 150kW 以 上电堆出货量将超过 400 套,其中出口近 100 套,我国领先企业的电堆技术参数已经和国 际先进企业接近。
电堆国产化率及技术指标提升,开发大功率系统难度降低。根据氢蓝时代动力科技有限公 司常务副总裁曹桂军在 2021 势银氢能与燃料电池产业年会上发表的《燃料电池系统开发 与多场景应用》的主题演讲,电堆的国产化率和技术指标快速提升。其中,单堆功率从 45~60kW 提升至 150~200kW;电堆功率密度从 2.5kW/L 提升至 4~4.5kW/L;关键零部件 国产化率从 50%提升至 90~98%;系统集成度从 300W/kg 提升至 450W/kg;环境适应性 普遍提高,一般可达到-30℃冷启动;基础材料不断突破,产业化加速,系统成本下降趋 势明显,电堆价格可低于 2000/kW,系统成本可低于 5000/kW。
电堆:初步实现产业化条件,国产化
2021 年电堆成本约占燃料电池系统成本 65%。膜电极主要包括催化剂、质子交换膜以及 气体扩散层,占电堆成本的 75%左右,其中催化剂占电堆的 36%,双极板占电堆的 23%, 质子交换膜占电堆的 16%。
膜电极:初步达到产业化标准,关键材料国产化推进带动成本下行
膜电极是燃料电池的核心部件,直接决定了氢燃料电池的功率密度、耐久性和使用寿命。 膜电极承担燃料电池内的多相物质传输(包括液态水、氢气、氧气、质子和电子传输), 通过电化学反应将燃料氢气的化学能转换成电能,直接决定了氢燃料电池的功率密度、耐 久性和使用寿命。其主要性能指标包括单位表面积的输出功率(功率密度)、贵金属用量 (单位功率输出的铂用量)、寿命和成本。具备高效多相传输能力的膜电极,能减少电堆 系统的辅机消耗,从而降低电堆成本,提高电堆系统可靠性。
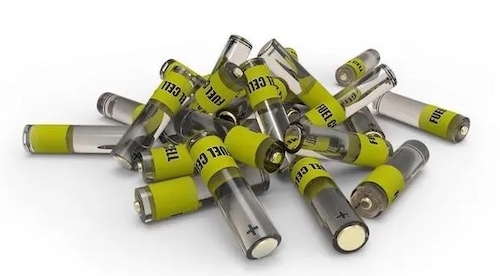
国内企业膜电极主要参数已经与国际先进水平接近,部分参数可以超过国外先进水平。目 前,国内已经有一批可以独立研发、生产膜电极的企业,从产品性能来看,主要性能参数 方面与国际水平接近,如部分领先企业功率密度可达到 1.4W/cm2,耐久可达 20000 小时 以上。国内领先膜电极企业鸿基创能、武汉理工新能源、擎动科技膜电极产品功率密度均 超过 1W/cm2,鸿基创能达到 1.4W/cm2,测试使用寿命超过 1~2 万小时,已基本满足产 业化应用需求。
21 年后国内膜电极企业扩产速度加快,双面直接涂布技术和膜电极一体成型技术正在成 为主流。国外膜电极供应商已具备膜电极批量自动化生产线,单线年产能在数千平方米到 万平方米级。2019 年后鸿基创能、擎动科技、武汉理工氢电以及泰极动力国产生产线先 后正式落成,我国的膜电极领域逐步开启批量化生产步伐。根据鸿基创能公司官网,鸿基 创能 2022 年将形成年产千万片的产能,公司开发了 CCM 阴阳极双面直接涂布技术和膜 电极一体成型技术,正在成为燃料电池行业膜电极涂布工艺的主流方向。
国产膜电极成本优势明显,并有望持续下降。国产化 MEA 产品规模化应用增强供应商议 价能力,大批量采购情况下上游原材料成本有望大幅下降,同时规模效应摊薄高昂的设备 投入,带动 MEA 成本下行。
膜电极关键材料-催化剂:低铂/高活性铂/非铂
催化剂起到分解氢气和氧气进行电化学反应产生电流的作用。催化剂根据贵金属铂的含量 分为铂催化剂、低铂催化剂与非铂催化剂。目前商用催化剂为铂碳催化剂,稀有金属铂的 高成本是燃料电池商业化的主要阻碍之一。催化剂需要平衡成本与耐久性两方面的需求, 新型高稳定、高活性铂或非铂催化剂是研究热点。铂合金催化剂已经取得很大进展,如铂 钴、铂镍等正在得到实际应用;非铂催化剂性能与稳定性还有待提升。
催化剂研发重点是新型制备技术、载体及接触界面改性。贵金属 Pt 的商业化能力较弱, 提高催化剂性能,需要在催化剂活性和结构设计方面取得突破。突破途径包括:1)设计 新型催化剂结构,如纳米笼、核壳、纳米框架、纳米线、纳米晶体,以提高催化剂比活性 或质量活性;2)对碳载体进行适当改性,如 N 掺杂,以确保离聚物非常均匀的覆盖,从 而增强质子传输;3)基于分子排列的碳载体和催化剂/聚合物界面的改性有望改善离聚物 分布和催化剂利用率。
降低铂载量是降低燃料电池电堆成本的重要途径。根据势银能链,国际领先企业目前单位 功率的铂载量从十年前的 0.8~1.0g/kW 降低到 0.1~0.4g/kW,铂催化剂用量的终极目标是 小于 0.05g/kW,即铂金属消耗量与传统内燃机尾气净化器铂金属用量持平甚至略低。目 前,国外催化剂用量已实现<0.2g/kW,而我国催化剂用量普遍处于 1.1g/kW 的水平。
目前我国铂催化剂以进口为主,国内正起步。日本田中贵金属、英国庄信万丰和比利时优 美科是全球较大的几家燃料电池催化剂供应商,催化剂制备技术处于绝对领先地位,已经 能够实现批量化生产(大于 10kg/批次),而且性能稳定,可靠性高。贵研铂业、武汉喜马 拉雅、中科科创、苏州擎动科技、武汉理工新能源等是国内开展催化剂开发的代表企业。 其中,贵研铂业是国际五大知名贵金属公司之一,在燃料电池催化剂领域布局较早,是行 业内唯一的上市公司。贵研铂业与上海汽车集团合作已经研发出铂基催化剂。根据公司官 网,苏州擎动科技开发的铂合金催化剂能够将燃料电池的铂消耗量降低 7%,是国内首个 实现量产的燃料电池用铂合金催化产品。
膜电极关键材料-质子交换膜:全氟磺酸膜是主流,国内具备量产能力
质子交换膜是膜电极核心材料,主要功能为传导质子、阻隔气体。质子交换膜在燃料电池 的主要功能有两个:一方面为电解质提供离子通道,一方面作为隔膜隔离两级反应气体。 此外,质子交换膜还需要对催化剂层起到支撑作用。质子交换膜性能的好坏直接决定着燃 料电池的性能和使用寿命。评价 PEM 的性能指标主要为离子基团当量值(EW 值)离子交 换能力离子传导率膜厚度气体渗透率机械强度以及成本等。理想的质子交换膜需要具 备高质子传导率,低电子导电率,气体渗透性低,化学、电化学、热稳定性好的优点。
全氟磺酸膜是目前主流质子交换膜方案。质子交换膜根据含氟情况进行分类,主要包括全氟 磺酸膜、部分氟化聚合物质子交换膜、复合质子交换膜和非氟化聚合物质子交换膜。其中由 于全氟磺酸聚合物具有聚四氟乙烯结构,其碳-氟键的键能高,使其力学性能、化学稳定性、 热稳定性佳,使用寿命远好于其他膜材料的使用寿命,同时由于分子支链上存在亲水性磺酸 基团,具有优秀的离子传导特性。全氟质子交换膜机械强度高,化学稳定性强,能够适应苛 刻的电池(电解池)的工作环境,对装置的电化学性能起到不可忽视的重要作用。
全氟磺酸膜产能国外垄断。全氟质子交换膜生产主要集中在海外,主要公司包括美国戈尔、 科慕、陶氏和 3M 公司,比利时索尔维公司,日本旭硝子玻璃、旭化成。美国戈尔公司在增强膜方面具有知识产权优势,每年 出货量达几十万平米,丰田 MIRAI、现代 NEXO 和本田 CLARITY 等都采用戈尔产品,国 内生产的燃料电池膜电极中,戈尔的增强复合膜市场占比达 90%以上。
国产质子膜已实现规模化应用,东岳集团加速国产化进程。根据氢能观察,2019~2020 年, 国产的质子交换膜均处于客户送样、测试验证阶段。国内目前少数成功实现质子交换膜商 业化量产的企业为东岳集团。东岳已成为继戈尔、科慕两家外国企业之后国内市场占比最 大的企业,具有原料、中间体、单体、聚合物膜全产业链,已建成全国唯一全氟酸质子膜 树脂合成生产线,实现量产并批量供货。当前产品已经进入奔驰公司的供应链体系,稳定 性、可靠性、寿命已经进入规模化验证中。
膜电极关键材料-气体扩散层:技术层面已经对标国际先进产品,规模化生产可期 气体扩散层(GDL)位于气体流场层和催化层之间,由碳纸和防水剂聚四氟乙烯材料构成, 以满足高导电性、高强度、高孔隙度、耐腐蚀、结构致密且表面平整等特点,起到支撑膜 电极、收集电流、传导气体、管控反应水(气)及热等重要作用。支撑层材料主要是多孔 的碳纤维纸、碳纤维织布、碳纤维无纺布、碳黑纸。
气体扩散层发展方向:1)设计具有梯度孔径的 GDL,以提高膜电极本身的传质能力。例 如,降低 GDL 一侧或两侧的孔隙率可以降低接触电阻并在 GDL 内部产生孔隙梯度,以促 进反应物供应和水分去除。2)采用“集成双极板-膜电极”或“无气体扩散层”设计,减 少或消除界面电阻,以同时满足导电、气体分配和水管理的要求。
规模化生产将带来气体扩散层成本大幅下降。根据 Strategic Analysis 数据,当生产规模 从 1000 套提升到 50 万套时,成本会从$2,661/套降到$102/套,因此批量化生产是实现气 体扩散层降本的关键。
我国气体扩散层技术层面已经可以对标国际先进产品,规模化生产可期。国外有日本东 丽(Toray)及三菱(Mitsubishi)、德国西格里(SGL)和科德宝(Feudenberg)、美国 AvCarb,韩国 JNTG 等制造厂商,都已实现气体扩散层的规模化生产,且都有多款适应 不同场景的产品销售。国内碳纸类材料的实验室技术可对标国际部分先进产品水平,有望 逐渐进入到产业化阶段,主要企业有中国台湾碳能、通用氢能、江苏氢电、江苏清能、上海河 森电气等。
双极板: 石墨双极板技术成熟,基本已实现国产化,耐久性和工程化有待验证
双极板是燃料电池电堆的核心结构件,起到支撑机械结构、均匀分配气体、排水、导热、 导电的作用。其性能优劣将直接影响电堆的体积、输出功率和寿命。双极板可分为石墨双 极板、金属双极板和复合双极板。石墨双极板具有质量轻、稳定性强和耐腐蚀性高等特点, 但机械性能较差;金属双极板具有机械性能强、厚度薄、阻气性好等特点,但易被腐蚀, 寿命较短。复合双极板则兼具石墨板和金属板的优点,但制备工艺繁杂,成本较高。金属 板(钛或者不锈钢等)较石墨板更利于实现小型化,从而有利于提高燃料电池电堆的功率 密度,表面改性的多涂层结构是金属双极板的主要发展方向。
石墨双极板技术较为成熟,基本已实现国产化,领先企业技术指标提前突破 2025 年国家目 标。国内石墨双极板技术近年来发展十分迅速,基本实现国产化。根据高工氢电的数据,目 前包括上海治臻在内的企业生产的国产金属双极板设计寿命已经超过 2 万小时;嘉裕碳素生 产的石墨双极板单面有槽厚度在 0.5mm,双面有槽厚度在 0.8mm,单组石墨双极板的厚度 在 1.3mm 左右,提前突破了国家制定 2025 年前单组石墨双极板厚度 1.5mm 的要求。
国内双极板企业扩产趋势明显,目前全国总产能超过 2000 万片。国内双极板重点企业扩 产趋势明显,2021 年 3 月上海治臻年产千万片级金属极板产线在常熟市投产,这是目前 全球最大的一条金属极板产线,根据高工氢电的统计,目前全国燃料电池双极板总产能已 超过 2000 万片/年。根据高工氢电的数据,2021 年国内主流双极板企业的出货量都有非常 大的增长。金属双极板领域已经出现了单个企业单个客户出货达百万片级别的现象;石墨 板市场各家出货也均有较大增长,表现明显的是原万片级出货企业的出货量级达到 10 万 片以上,头部企业的出货了 50 万片/年以上。
系统部件:技术成熟,国产化程度相对较高
空气压缩机:已实现全功率段国产化,国产化率接近 100%
离心式空压机成为主流选择。空气循环系统的关键部件为空压机,也为燃料电池阴极供气 系统重要部件,通过对进堆空气进行增压,为电堆提供适量适压的氧气。空气压缩机的性 能对燃料电池系统的效率、紧凑性和水平衡特性等有着重要影响。燃料电池系统用空压机 主要有离心式、罗茨式、螺杆式三种类型。由于离心式空压机在效率、噪音、体积、无油、 功率密度等方面具有良好的综合效果,故随燃料电池系统功率的快速上升,离心式空压机 已逐渐成为市场上的主流选择。在空气压缩机的关键部件中,轴承、电机是瓶颈技术,低 成本、耐摩擦的涂层材料也是开发重点。
空气压缩机有效提高发电效率降低燃料成本。车用燃料电池使用的空压机主要有螺杆式压 缩机和涡轮式压缩机等。根据《车用燃料电池专用空压机的现状分析》,螺杆式空压机的 优点是压力/流量可以灵活调整、启停方便、安装简单,缺点是噪声大、体积大、质量重和 价格高,已在美国 GM,PlugPower、加拿大 Ballard 等公司的燃料电池系统中采用。涡轮 式空压机容积效率较高,压力与气量连续可调,但尺寸和重量较大,本田和现代等公司已 定制开发了空气轴承的涡轮式空压机。目前,国内已经完成 30kW 级实车验证,国际一流 水平已经完成 100kW 级实车验证。
氢气循环泵:2020 年氢循环系统市场逐步实现国产替代
主动循环形式的氢循环泵成为主流,引射器使用量逐渐增长。氢气循环系统的作用是将电 堆未反应的氢气再次循环到电堆的氢气入口,从而提升氢气的利用率及涉氢安全,同时将 电堆内部电化学反应生成的水也循环至燃料电池堆的入口,改善电堆湿润水平和提高水管 理能力。氢气循环系统分为主动循环和被动循环两种形式,主动循环形式的关键部件是氢 气循环泵,被动循环形式的关键部件是氢气引射器。氢循环泵在主动可调节、快响应速度 和宽工作区间等方面占有一定优势,成为未来使用主流。根据高工氢电,2020 年国内氢 循环系统有引射器和氢气循环泵两种产品,其中引射器的使用量约占氢循环系统出货量的 11%。
2020 年以后我国氢循环系统市场逐步实现国产替代,国产氢气循环泵技术达到国际领先 水平。根据高工氢电,2020 年前,普旭占据了国内约 90%的市场份额。2020 年以后我国 氢循环系统市场逐步实现国产替代,普旭基本退出国内市场。上海政飞的 DQ30/DQ60 在 功率、流量、温度范围等方面优于普旭公司产品。
增湿器:材料端技术门槛较高,国产替代任务艰巨
目前我国增湿器仍以进口为主,韩国科隆是行业内龙头公司,主要核心技术壁垒是膜管材 料的研发突破。燃料电池电堆在反应过程中,质子交换膜需维持一定的湿度以保证较高的 反应效率,因此要求反应介质需携带一定量的水蒸气进入电堆,这一步通常需通过增湿器 来实现。沃瑞氢能、鸾鸟电气、同优汽车、魔方新能源等国内企业陆续取得产业化突破, 具备一定价格优势,大规模国产替代需要依靠材料技术的长期协同进步。
燃料电池制备工艺复杂,膜电极&双极板设备价值量高
燃料电池电堆生产流程主要包含膜电极组件制备、双极板制备和电堆装配三大环节。具体 来看:1)膜电极制备:主要涉及管式炉、搅拌、涂布、贴合、热压和模切设备等;②双 极板制备:2)石墨双极板生产涉及模压、浸渍和 CNC 设备等,金属双极板生产涉及冲压 (蚀刻、液压)、清洗、激光焊接和 PVD 等设备;3)电堆装配过程:主要涉及密封、堆 叠、活化和测试等设备。
燃料电池与动力电池生产工艺共通性较强,多家锂电设备企业重点布局燃料电池领域。燃 料电池与动力电池生产工艺具备较强共通性,根据高工氢电的数据,国内已有多家锂电设 备企业重点布局燃料电池领域,例如:1)先导智能于 2021M3 发布燃料电池智能制造整 体解决方案;2)科恒股份的质子交换膜涂布设备已形成批量销售;3)星云股份于 2018M8 推出首条燃料电池膜电极处理自动装配线等。除了部分锂电设备企业进行横向延 伸布局,本土燃料电池市场还涌现出魔方新能源、苏州世椿、隆深机器人等企业。(报告来源:未来智库)
3 竞争格局:打好示范期的突围赛
多家厂商入局,市场集中度持续下降
2019~2021 年市场集中度维持高位,基于对政策和未来市场前景的良好预期,进入燃料电 池系统行业的企业持续增加,市场集中度有下降趋势。2016-2021 年 6 月末累计配套车辆 上牌的 TOP5 分别是上海重塑、亿华通、大洋电机、国鸿氢能(鸿力氢动)、百应能源, TOP3 和 TOP5 市占率分别为 51%和 66%,集中度较高。新进入企业在示范期间激烈的竞 争中能否存活下来,存在较大不确定性。
2019 年至 2021 年期间燃料电池电堆的 TOP3 集中度从 84%降低到 58%,市场集中度持 续下降。
根据香橙会研究院的统计,2021 年亿华通是北京冬奥会最大的受益者,成为 2021 年度上 牌数量最多的燃料电池系统厂商,市场占有率高达 29%;海卓动力(青岛)和上海杰宁订 单主要来自于本地的氢能重卡示范项目;国鸿氢能(鸿力氢动)系统产品主要配套美锦能源 在国内多地区的示范项目;捷氢科技上牌订单较为分散,配套车型囊括重卡、城市客车、客 车和乘用车。
国内外厂商积极扩产能
受到燃料电池汽车示范政策落地驱动,国内燃料电池企业开始积极扩产,现代汽车、巴拉 德、丰田国外领先企业也积极在华合资建厂。包括博世(中国)、重塑科技、清能股份、 国创氢能、国鸿氢能、氢璞创能、新氢动力、未势能源、氢途科技、东方氢能、爱德曼、 浙江润丰、中船 712 所、大洋电机、恒动氢能等。
产品方面,提升系统功率和功率密度
上牌车型平均功率持续提升。高工氢电数据显示,从上牌车型的燃料电池系统功率来看, 2019-2021 年上牌车型平均功率依次为 39.6KW、52.9KW 和 93.2KW,其中 2021 年的系 统功率水平在国家示范群补贴政策的引导下出现显著提升。分车型看,2021 年上牌燃料 电池客车车型平均功率达到 80KW 左右,燃料电池重卡车型平均功率达到 110KW 左右。
主流厂商系统的功率密度已经远超燃料电池技术发展路线中规划的水平,技术发展速度快 于预期。根据高工氢电,这些已达成的技术指标与燃料电池技术发展路线中规划的功率密 度 350W/kg 相比,已经优于该目标 1.6 倍到 2.0 倍;在功率密度方面,上海重塑 Prisma 镜星 12+与亿华通 G80Pro 的质量功率密度为 702W/kg、550W/kg,国鸿氢能鸿途 G110 的质量功率密度达到了 555W/kg。在额定功率方面,上海重塑 Prisma 镜星 12+、上海捷 氢 PROMEP4H、雄韬股份 VISH-130B 相关产品达到了 130kW,头部企业技术优势明显。
来源 【未来智库】:https://baijiahao.baidu.com/s?id=1725062512982411549&wfr=spider&for=pc
平台声明:该文观点仅代表作者本人,氢能网系信息发布平台,我们仅提供信息存储空间服务。
发表评论 取消回复