PCBFC的差异化优势和简化系统架构的能力源于一个核心基本因素:介电材料(一种特殊类型的绝缘体)组。印刷电路板材料本身就是介电材料——它们被设计为在同一平面内具有导电和不导电区域;这就是典型的印刷电路板电子板的工作原理。Bramble Energy 基于 PCB 的燃料电池不仅可以在全球任何一家 PCB 工厂制造,而且还采用了与标准 PCB 制造相同的材料和工艺,所以可以大范围利用原有PCB的固有产能。
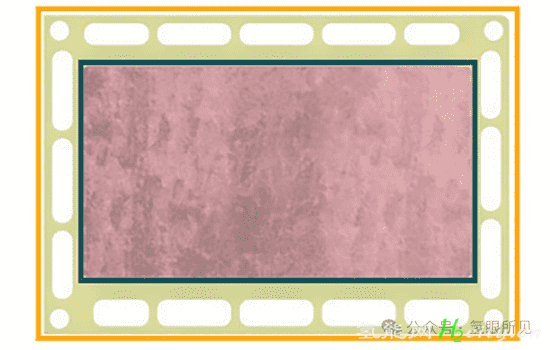
图1所示。单个PCBFC™模块的示意图,显示绿色的导电铜表面和黄色的不导电FR4。
●可定制的电压电流图;
●非导电冷却剂通道;
所有燃料电池都是由单电池堆叠在一起(称为电池堆)组成的,每个电池的工作电压通常为 0.6 V左右,电池数量越多,整个电池堆的电压就越高。例如,一个典型的石墨或金属板燃料电池,其运行功率约为 100 KW,那么它可能有约 300 ~400 片单电池,300 ~400 个单电池,每个电池提供 0.6 伏电压,因此工作电压约为 180 ~240 V(通常这个范围会更大)。当我们将其与电压为 400V 或 800V 的电池组组合成混合动力系统时,我们必须安装一个DC/DC升压转换器,将燃料电池的输出电压提高到为电池组充电所需的电压。
DC/DC转换器可被视为升压变压器,以确保稳定的输出电压。DC/DC转换器是一种定制的、比较贵的重型组件,体积较大,会占用车辆空间。在升压配置中,直DC/DC升压转换器的电气效率可能低于其相反模式,即从较高的输入电压降至较低的输出电压。
在设计 PCBFC™ 电堆时,考虑到这些因素,并确定了一种方法来提高整个电堆的电压,同时为给定的电堆提供相同的功率输出。这一优势的设计是PCB 材料组合所固有的,同时也符合降低成本的目标。
PCBFC™中使用的介电材料允许在单个平面(或者我们称之为模块)内分割MEA,从而增加该平面上的电压。如下图2所示:
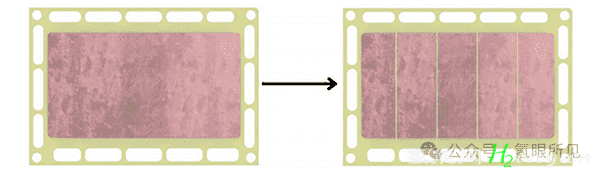
PCBFC™ 可以安装一个分成五个不同部分的 MEA;因此,该模块的电压从 0.6 V 提高到 3 V,同时提供相同的功率输出。当我们将这些模块组装成一个堆栈时(如下图3所示),燃料电池的电压曲线就会比金属板或石墨板的预期电压曲线高出五倍。
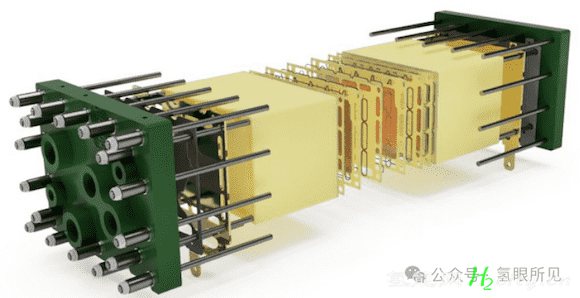
图3:整体装成电堆效果图
如果我们考虑之前的例子,即由约 350 块板组成的典型 100 kW 堆,工作电压约为 210 V,那么我们现在可以比较由约 350 块板组成的 100 kW PCBFC™,其工作电压约为 1050 V。如下表1所示,显示了如何利用 MEA 分段来生产功率为 30 ~100 kW、输出电压约为 1000 V 的电堆。
表 1. PCBFC™ 电堆在约 1000 V 高电压输出目标下的功率变化

燃料电池堆可在客户指定的电压下运行,通过将燃料电池的工作电压与电池组的工作电压相匹配,该燃料电池堆具有以下优势:
1. 简化的降压型 DC-DC 转换器可降低成本并提高电气系统效率。
2. 使用现成的低成本系统元件。
3. 降低系统质量和体积,通过更细的电缆和更小的 DC/DC 元件尺寸提高集成度。
在某些情况下,我们可以更进一步。根据运行参数,可以通过模块设计将DC/DC转换器一并去掉,在这种结构中,负载管理装置可以获取燃料电池电压,并将其直接接到电池上。在这种运行模式下,虽然对充电电路的控制较少,但燃料电池的功率会跟随电池组的曲线变化,最终进一步降低系统的质量、体积、成本和复杂性。
使用 PCBFC™ 技术可以实现上述优势,因为燃料电池的介电结构允许在单个燃料电池模块内细分电气区域,并为调整电池的电流和电压输出提供了可能性,而不受有效面积和电池数量的影响。单个模块将由子电池组成,这些子电池可以以各种配置连接,从而根据应用的特定需求调整电力输出。
为了确保低温PEM燃料电池堆的最佳运行,它需要在80°C下运行(根据不同MEA温度可能有差异)。根据经验,系统可以以50% ~65%的效率运行,因此产生的热量必须由系统散掉。
由于燃料电池系统可能会产生大量的热量,因此有一个有效的冷却回路是很重要的。与内燃机(ICE)不同,燃料电池系统在尾管处的热量排出量要低得多,因此,冷却系统通常在相对较低的温度下运行。燃料电池冷却回路的典型原理图如下图4所示,它由冷却剂胶管、电动冷却剂泵、电动冷却剂阀或恒温器、冷却剂加热器(在寒冷条件下快速加热电池组)、散热器和膨胀水箱组成。准确的BOP组件也会因电堆或者控制差异而不同。
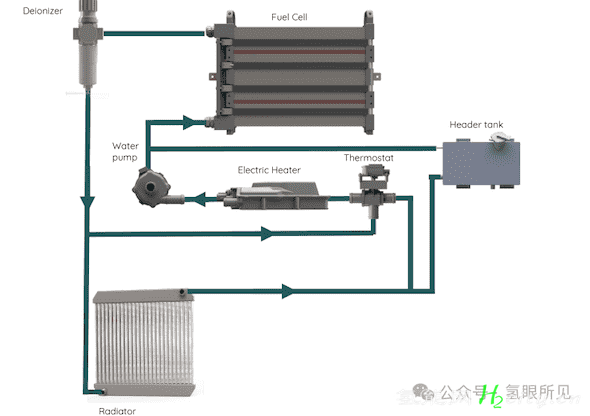
传统的金属或石墨板燃料电堆有较复杂的冷却回路,需要去离子水作为冷却介质。这是因为在这些结构中,构成电堆的(双极板)是导电的。因此,为了避免通过冷却液使电堆短路,通常的做法是使用低导电性的冷却剂。因此,通常是选择去离子水(或冷却液)作为这些系统的冷却介质。在典型的燃料电池运行中,除离子器被放置在与冷却剂流动一致的位置,通过电导率传感器不断监测冷却剂流动,以确保安全运行。除离子器通常需要定期更换,会产生较多的维护费用,并导致停机时间和用户成本增加。
然而,对于PCBFC电堆,构建冷却剂通道的FR4材料是电绝缘的。整个冷却剂通路由不导电的FR4材料构成,并与导电铜表面和通路隔离。这就没有冷却水需要去离子的要求,以及维护去离子冷却水所需的在线去离子器和传感器。PCBFC™可以用水乙二醇混合物冷却,也可以放入现有的混合冷却结构中。
去除去离子水回路和去离子器可以简化复杂的燃料电池系统,因为专门用于冷却剂回路的热交换器和散热器也可以去除。由此得到的简化系统具有较低的运行功耗、质量、体积和成本。减少组件数量直接对应于降低系统的维护和资本支出成本。
在传统的燃料电池堆中,双极板由导电材料组成,并被膜电极分开。因此,通过单元对单元的连接来防止堆栈外部表面短路是至关重要的。这需要在堆栈集成过程中考虑额外的安全问题,从而导致系统设计更加复杂,增加了总体成本、质量和体积。
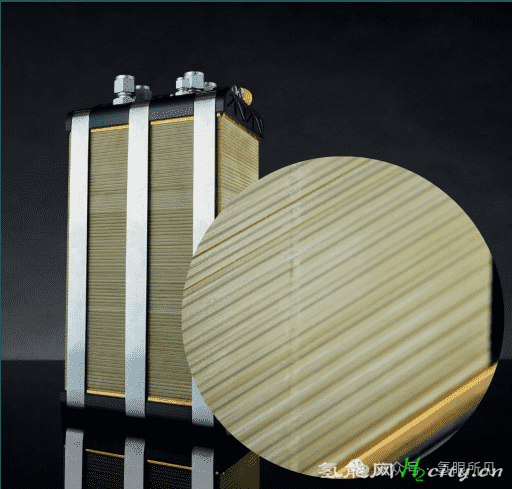
在开发 PCBFC™ 堆栈技术的过程中,Bramble 解决了基本的系统架构问题,对已经处于行业领先地位的成本途径没有任何额外影响。这些优势源于 PCBFC™ 结构中使用的介电材料,并直接影响到系统的电气效率、封装外壳和成本。
另,作为这项研究的一部分,Bramble Energy 将把电解槽膜技术的最新进展与印刷电路板行业的制造能力结合起来。印刷电路板电解槽 (PCBEL™) 将为绿色制氢提供低成本、耐用和高效的下一代水电解槽。利用印刷电路板平台开发电解槽技术可实现模块化、耐用的电解槽设计,并可利用现有的印刷电路板制造设施和供应链,以低成本快速扩大规模。见下图6:
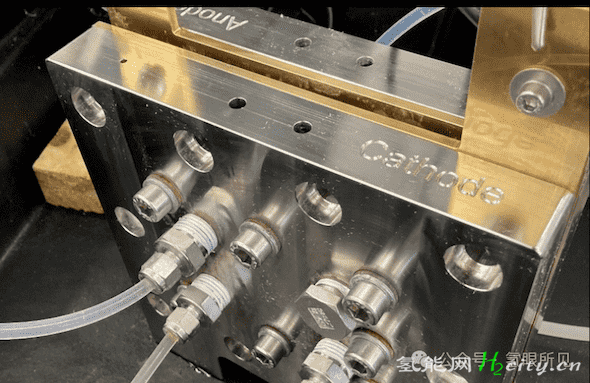
与传统电解系统相比,PCB 平台大大简化了电解槽的设计,减少了部件数量,降低了制造成本和运行过程中潜在故障点的数量。Bramble 将优化 PCB 电解槽的性能(包括长期测试),并开发模块化、可扩展的电解槽系统设计。
来源:氢眼所见
平台声明:该文观点仅代表作者本人,氢能网系信息发布平台,我们仅提供信息存储空间服务。
发表评论 取消回复