1、国内氢能政策
2、国内可再生氢项目
3、国内氢能应用领域
4、国内氢气成本
5、氢能产业链
6、重点企业分析
应用核电进行碱性电解水制氢经济性分析
利用核电厂在电力富裕时电解水获取氢气,在用电高峰时,由氢燃料电池发电,可以提高核电参与电网调峰的能力。对比现有氢气获取方法,碱性电解水制氢技术安全可靠、经济性能好,适应用于核电大规模氢能项目。本文详细介绍了现有碱性电解水制氢系统主要组成部分,核算了采用碱性电解水制氢系统进行核电制氢的成本预估,结果表明,一套1000m3/h的碱性电解水制氢设备需一次性投入877万元,投资回报年限为1.8年;若自行购置氢气压缩机则需投资1277万元,投资回报年限为2.58年;系统年运行费用为204.5万,回本后年利润为495.5万元。
一 引言
氢是一种清洁能源,与电力相比,更容易储存和输送,可以用于所有一次能源和电力生产的能源载体[1]。
氢能作为一种二次能源,需要利用一次能源来生产,以可持续的方式实现氢的大规模生产是实现氢利用的前提[2]。点击加入氢燃料电池产业交流群及通讯录目前,核电已经成为世界电力供应的重要方式,电网对核电参与调峰的需求随着核电机组发电量的增加而增加,利用核电厂低负荷制氢,在电力富裕时电解水获取氢气,在用电高峰时,由氢燃料电池发电,有助于核能的可持续发展,可以为核能在电力生产以外领域的应用开辟道路。
利用核能制氢对于我国实现碳中和具有重要意义。现有核能制氢技术主要分为甲烷蒸汽重整制氢、高温蒸汽电解制氢、热化学循环制氢、碘硫循环制氢与常规电解水制氢[3]。相比于电解水制氢,其它制氢方法需要输入大量热量,反应多需要在800℃以上高温环境中进行,制氢过程通常需在核反应堆内进行,相关技术多处于试验阶段,存在一定的安全隐患。电解水制氢技术则更为成熟,在大量廉价电力供应的情况下具有经济优势和技术优势,可以满足核电大规模应用的场景。
二 电解水制氢
(1) 氢气获取方法
如表1所示,目前常见的制氢方法主要分为化石能源制氢、电解水制氢、工业副产氢、生物质制氢以及光催化制氢[4]。工业中,水蒸汽通过灼热的焦炭得到氢气可以获得纯度为75%的氢气;水蒸气通过灼热的铁可以获得纯度为97%的氢气;相比而言,电解水制氢可以获得纯度相对较高的氢气,纯度可以达到99%以上。
因此,采用核电低谷电制氢,不仅可以获得高纯度氢气,还可以提高电网调峰能力,有助于提高电网运行的经济效益。
(2) 电解制氢方法
电解水制氢采用直流电把水分解为氢气和氧气[5]。具体的方法是:在一些电解质水溶液中通入直流电时,被分解的是作为溶剂的水,普通纯水为典型的弱电解质,具有电离度小,导电能力弱的特点,需要加入类似于氢氧化钠、硫酸、氢氧化钾等电解质以提高溶液导电能力。
现有电解水制氢技术按照电解槽种类可以分为:固体氧化物电解水技术、质子交换膜技术和碱性电解水制氢技术[6]。点击加入氢燃料电池产业交流群及通讯录在工业应用中,质子交换膜技术和固体氧化物技术存在电解槽造价高、经济性差的缺点。相比之下,碱性电解水制氢技术的电解槽结构简单、技术成熟、价格普遍较低,其应用更为广泛。另外,该技术获取氢气也存在便于维护、使用寿命长、经济效益好的优点,比较适合应用于核电站大规模氢能项目[7]。
(3) 电解制氢设备组成
相比于利用核反应堆高温余热进行制氢的方法,电解水制氢系统可以用厂用电变压器接出一路直接进行电解水制氢,可在核岛外专门搭建电解水制氢的车间。制氢设备组成为:主体设备,辅助设备及电控设备。主体设备组成:电解槽,附属设备一体化框架。辅助设备组成:水箱,碱箱,补水泵及减压分配框架等。电控设备组成:整流柜,配电柜等[8]。
电解液循环系统:连通管收集得到氢氧分离器分离出的碱液,在循环泵加压的作用下,碱液过滤器去除溶液中的杂质,后经电解槽来参与下一次电解反应,形成闭环系统。洗涤器中洗出的碱液可由溢流管返回气液分离器。
氢、氧气体系统:从电解槽出来的氢气碱液混合体经换热器降温,进入氢分离器后,在重力作用下进行气液分离,氢气由上层管道进入氢洗涤器,经洗涤器冷却、洗涤以及捕滴网捕滴,最大限度减少气体中的含碱量和含水量,最终经薄膜调节阀放空或进入纯化装置。氧气处理过程与上述过程相同。
碱水补给系统:随着制氢设备的运行,系统内的水不断消耗并体现在氢氧分离器的液位不断下降,当液位低于系统设定值时,系统内的加水泵就会自动启动,将水箱中的水注入氢(氧)洗涤器并溢流至分离器中,当分离器液位上涨至设定上限时,加水泵自动停止工作;当碱液的浓度下降时,也可以将碱箱中少量碱液直接打入电解液循环系统。
冷却水系统:冷却水经冷却水总管道分两路进入系统,一路冷却水经气动薄膜调节阀进入碱液换热器,带走其热量,通过不断调节薄膜阀开度,保证电解槽的温度始终维持在85℃左右;另一路冷却水进入氢、氧洗涤器中,来冷却产生的氢气和氧气,确保出口气体的温度在40℃以下。
三 电解水制氢成本核算
目前市场上较大的单台制氢设备的能力为1000
m3/h,产氢量为1200m3/h与1500m3/h的设备尚未大规模量产。以建造一台1000m3/h电解水制氢系统为例,按照系统年运行时间为2000h计算,年产氢量为200万Nm3,制氢系统投资为850万元,因为电解槽用碱属于危险品,需要自行购置,一次性用碱7t,平时补充碱量较少。建设一台电解水制氢厂房为20万元,设备年用电量为1018万千瓦时,按照低谷电价为0.17元/千瓦时计算,系统电耗成本为174万元/年。系统每年可生产氢气200万Nm3,每年可生产氧气100万Nm3,含纯化设备,可以获得99.999%的高纯氢,制氢需要采用纯水,每小时消耗纯水1t,2t自来水可制的1t纯水,按照水费为3.6元/吨计算,年用水成本1.5万元。根据设备使用寿命20年计算,年折旧成本为43.85万元,年维修成本为5万元。由于设备便于维护,可以配备2人专门简化,年人工成本为24万元。出口氢气压力为1.6MPa,单台制氢设备不包括氢气压缩机、加压站等的成本。一台20MPa氢气压缩机需要200万元,共需两台,一台工作,一台预备。电解水制氢系统收入与成本分析如表2,单台1000m3/h碱性电解水制氢设备需一次性投入877万元,系统年运行费用为204.5万,电费成本占比达到85%,回本后年利润为495.5万元,投资回报年限为1.8年;若自行购置氢气压缩机则需投资1277万元,投资回报年限为2.58年。
一般电解槽出来的氢气是99.9%的纯度,经过纯化设备后可以达到99.999%高纯氢的要求,能够满足加氢站对氢气的要求。1kg氢气体积为11.2m3,市场售价在40~60元,售价在3.57元/m3~5.36元/m3之间。电解水制氢设备通过纯化设备后得到氢为高纯氢,售价较高,罐装后的价格为35元/瓶,每瓶5m3,售价为7元/m3,出厂价为3.5~4元/m3。目前电解水制氢获得的氧气都是直接排掉,主要存在两方面考虑:(1)市场上的氧气大多通过空气分离获得,生产成本低,氧气压缩机价格高昂,收集成本较高,氧气售价低,经济性差;(2)氢气跟氧气同时生产、罐装存在很大的安全隐患,一般不会通过安全部门的审核。
四 结果
根据核算结果,建立一套1000m3/h碱性电解水制氢设备需一次性投入877万元,投资回报年限为1.8年;若自行购置氢气压缩机则需投资1277万元,投资回报年限为2.58年;系统年运行费用为204.5万元,电费成本占比达到85%,回本后年利润为495.5万元。当电价在0.3元/千瓦时以下时,碱性电解水制氢存在利润。另外还要考虑储存、运输等环节对制氢价格的影响,输运成本占总成本的30%,制取的氢气可以考虑管道短途运输,输送到50~100公里内的居民用户或者化工厂就近消纳。
七合一气体扩散层(GDL+MPL)制作工艺
气体扩散层(GDL)是由多孔、且非编织特性的碳基材组成,基材经过 PTFE 疏水处理后,涂布单层或多层的微孔层(MPL),形成具有不同孔隙的多孔结构。
下图为气体扩散层三维结构示意图,其中具大孔结构的碳纸基材标示为绿色,PTFE 疏水材为黄色,最上层的微孔结构标示为蓝色 。一般而言,燃料电池气体扩散层材料具有以下关键特色,这些特性之间除了有基本功能考虑,部分存在竞争关系,在材料设计与选用时,皆需纳入做通盘考虑。
气体扩散层之三维结构
反应气体扩散: 气体扩散层要能传递反应物(氢气、氧气),确保 足够的反应物可快速且均匀的扩散至催化剂层,以进行电化学反 应,因此,气体扩散层的孔径必须够大且这些孔隙需具备足够的疏 水特性以避免燃料电池的产物水阻塞孔道。
产物扩散与传输: 气体扩散层需有效的将液态水自催化剂层移至 流道板,以避免让液态水阻塞了反应物的扩散通道。然而,排水的 特性需要被优化设计,如果排水能力太高,则将导致质子传导膜 太干而产生脱水,进一步将使得质子交换膜的质子传导率下降。
导电特性: 气体扩散层材料导电特性越高越好,这有助于减少电子传导过程的奥姆损失,帮助电子在催 化层和集电板之间传递。然而,调整气体扩散层的其他物理特性时,都会影响到材料的导电特性,例如 增加气体扩散层的孔隙率以及 PTFE 含量时,都将使得导电特性下降。一般材料的导电特性还可以藉由碳 材料的热处理温度进行改善。
导热特性: 膜电极组(MEA)反应产生的热/冷,需由气体扩散层传导至双极板上,同时也须保持膜电极组 均匀的温度分布。热量的局部累积将会对电池电极反应、质子传导膜的奥姆损失以及水的挥发与冷凝产 生直接的影响。
机械支撑性: 在膜电极组中,气体扩散层也扮演支撑膜电极组的角色,用来保护催化剂和质子传导膜, 避免气体流道的压力差而损伤膜电极组,也避免质子传导膜在电池加压组装时陷入流道板而造成损坏。
下面介绍七合一的气体扩散层(GDL+MPL)制作工艺
Step 1.切碎碳纤维
切碎碳纤维的工艺流程示意图
Step 2. 有机纤维碳化
有机聚合物经过纺丝和稳定之后通过高热解温形成碳纤维,热解在温度高达1100-1350℃的惰性气体中进行,材料释放出大量的氢气、氮气和氧气等气体,形成碳质量分数在90%以上的碳纤维制品。
Step 3. 造纸/织布工艺
将碳纤维进行分段剪切并在专门的溶液中进行分散,接着用类似造纸的工艺将碳纸成型,成型后的碳纸再经过树脂(热固性树脂如酚醛树脂等)浸渍和硫化,这一阶段的工艺基本决定了碳纸的厚度、孔隙率以及孔隙分布的各项特性。
Step 4. 石墨化
成型的GDL被加热到2200-3000℃(也有说是在1400-2000℃)完成石墨化,这个阶段非常重要,通过石墨化以后扩散层会在导电、导热以及机械强度方面得到全面提升,而且扩散层的化学稳定性以及表面物理稳定性更强,因此石墨化的程度是一非常关键的标准。
Step 5. 疏水处理
这一阶段主要进行PTFE(PTFE类、氟乙烯、丙烯FEP)溶液的浸渍、烘干以及烧结。燃料电池优化的核心就是水热管理,扩散层疏水处理对燃料电池工作过程中能够顺利排出生成的水,同时又不阻碍反应气体扩散起着很重要的作用,GDL的疏水性要弱于MPL层,形成水力梯度以防止水淹。
Step 6. MPL层涂布
最后通过喷涂、丝印或沉积的方法将MPL层乳液涂布在GDL层上,最终烧结形成气体扩散层,乳液的原料的配比对MPL层孔隙率以及疏水性能有着重要影响。
Step 7完整的GDL与前制程加工好的MEA贴合
氨能源技术开发前景
1引言
由于化石燃料的大量使用,能源枯竭和气候恶化已成为21世纪人类面临的两大难题。为了应对这些威胁,各国陆续制定了新能源发展战略和减碳目标。根据国家统计局的数据,2021年我国能源消费总量为52.4亿t标准煤(SCE),其中,作为碳排放大户的煤炭占能源消费总量的56.0%,而清洁能源(如天然气、核能、水电等)仅占比25.5%,这离实现“双碳”目标还有一定距离。
由于氢气的燃烧热值高,约为天然气的3倍,且燃烧后不产生碳排放,因此氢气被认为是一种极具潜力的新型绿色能源。在过去数十年的发展历程中,已开发出了多种类型的储氢材料,但市场上大部分氢气产能仍严重依赖甲烷重整、烷烃脱氢等化石燃料制氢工艺,使得制氢环节不可避免地产生碳排放,造成氢能“越发展,越污染”的窘境。另外,电解水作为最理想的制氢方式之一,该过程的产物中只含有氢气与氧气,但电解成本始终居高不下,难以得到大规模普及。
氨作为一种工艺成熟、成本低廉的非碳基储氢材料,在-33℃/0.1MPa的条件下就能以液态形式进行储存与运输,可以有效突破氢能的发展瓶颈,具有极大的研究价值。另外,目前在合成氨领域的研究已开始由传统的haber-bosch工艺逐步转向光/电催化固氮,在降低生产成本的同时,还可避免使用工业副产氢作为原料,实现真正意义上的零碳制氢。除了用作氢载体,氨还可以直接以燃料的形式进行利用,在这方面的研究也越来越多,并且在工业上已经取得了一定的突破。本文中从氨裂解制氢、直接燃烧、燃料电池等方面对氨能展开了系统的综述。
2 氨裂解制氢
1904年,Perman等发表了第一篇关于氨热裂解反应的报道,他们发现在1100℃以上的高温环境中氨近乎完全裂解为氢气和氮气。早期对氨裂解反应的研究主要是为了促进合成氨工业的发展,但随着人们对储氢材料的开发,氨裂解反应逐渐成为研究热点。氨裂解反应方程式如(1)所示。
2NH3⇌N2+3H2,∆H=+92.4kJ/mol(1)
2.1氨裂解催化剂
氨裂解与合成氨为互逆反应,合成氨催化剂在理论上也适用于氨裂解过程,且这一推论已得到广泛证实。Ganley等[4]对单金属催化剂进行了系统研究,发现在氨裂解反应中不同金属催化剂的活性排序为Ru>Ni>Rh>Co>Ir>Fe>Pt>Cr>Pd>Cu>>Te、Se、Pb,但即使是活性最高的Ru基催化剂,在低温下仍远未达到反应的热力学平衡。除了传统的单金属/合金类催化剂,近几年氮/碳化物、金属酰胺及酰亚胺等材料也展现出优异的氨裂解催化性能。Huo等利用SBA-15的空间限域效应,将Mo2N负载到SBA-15/rGO复合载体上,得到高度分散的催化剂,氨裂解速率达到30.58mmol/(g·min),性能可与Ru基催化剂相媲美。中科院大连化物所陈萍团队研究了BaNH、CaNH和Mg3N2在氨裂解反应中与Co的协同作用,发现在金属Co和BaNH相的界面处形成了[Co-N-Ba]中间物质,从而促进了氨气的裂解。各类氨裂解催化剂的制氢性能如图1所示。
2.2氨裂解反应器
氨裂解反应是一个结构敏感的体积增大过程。因此,设计一个合适的反应器可以有效提高低温下氨的裂解效率,同时将产生的氢气转移,促进氨裂解反应正向移动。Badescu等采用一维模型,研究了填充床反应器的最优化设计方案,发现通过改变反应器的形状或沿轴向控制催化剂颗粒的大小可以提高氨裂解催化性能。Itoh等开发了一种高效管壁催化膜反应器,该反应器主要由管壁催化剂和钯膜管组成,氨在催化剂表面裂解后,产生的氢气经过钯膜分离提纯,在375℃下实现了近100%的氨转化率。Badakhsh等首次提出了通过焦耳加热机制分解氨的紧凑型催化泡沫反应器,该反应器具有体积小、效率高和功率密度大等优点,与外部加热相比,使用焦耳加热机制后反应器的比活性提高了10倍。
2.3待突破的关键技术
尽管利用氨作为储氢载体可以解决氢气储运难度大、成本高等行业痛点问题,但目前该方式也存在许多不容忽视的制约因素:①氨裂解反应所需温度较高,远未达到低温下的热力学平衡,能量损耗大且不利于分布式应用;②催化剂的研发很难脱离合成氨催化剂范畴,所使用的非贵金属普遍存在活性不足等问题,而贵金属催化剂成本高,高温下易汽化,造成活性组分损失;③高温裂解过程中产生的H2会使高分散的活性中心发生迁移团聚,催化活性迅速降低。因此,开发温和条件下的高效氨裂解催化剂引起了学者们的广泛兴趣。
3氨直接燃烧
氨的储能特性与甲烷类似:甲烷通过4个C-H键的断裂重组来释放能量,氨拥有3个键能相近的N-H键。如方程式(2)、(3)所示,二者的关键区别在于甲烷燃烧会产生碳排放,而氨燃烧后的理想产物为对环境无害的氮气,且氮气可回收作为合成氨的原料,形成一个氮循环过程。因此,氨可能会成为未来化石燃料的替代能源之一。
CH4+2O2⟶CO2+2H2O,∆H=-889.6kJ/mol(2)
4NH3+3O2⟶2N2+6H2O,∆H=-1268kJ/mol(3)
3.1氨-氢混燃
1965年,Samuelsen等研究了火花式发动机中氨-空气火焰的火焰传播速率,发现氨的火焰传播速率要慢于异辛烷,维持稳定燃烧状态较为困难,这可能是氨的燃点较高导致的。Han等测量了氨-氢-空气火焰的层流燃烧速度,发现在0.7~1.6的宽当量比范围内氢气对氨火焰均具有增强作用。此外,He等在同一个发动机系统中对不同燃料的燃烧情况进行分析,其中,氨-氢燃烧的大部分特性与碳氢燃料相似,只是热值相对较低。Comotii等基于氨的储氢特性,将装有钌基催化剂的氨裂解反应器与发动机耦合,通过裂解产生的氢进行助燃,成功实现了氨的稳定燃烧,且热效率与汽油发动机相当。尽管氢的添加可以显著提升氨燃料的燃烧效率,但也存在着一些现实问题,如氮氧化物排放等。例如,Khateeb等在涡流燃烧器中证实了掺氢量与火焰稳定性正相关,但当氢的体积分数增加到20%时,尾气中NOx的体积分数达750×10-6。因此,当选用氢/氨比较高的混合气体作为燃料时,可能需要在尾气处理部分安装烟气脱硝(SCR)装置,以利用燃烧残余氨除去NOx。
3.2氨-甲烷混燃
天然气在三大化石能源中相对最为清洁环保,目前国外针对甲烷掺氨混燃做了大量的研究工作,以进一步降低天然气燃烧的碳排放。2016年,Valera-Medina等在旋流喷射装置中进行了氨-甲烷混合物燃烧试验,发现2种气体分子的混合燃烧过程非常复杂,火焰的稳定性与尾气中CO浓度直接关联,且富燃条件下的试验结果更好。Ji等在钝体旋流燃烧器上进行了3种甲烷组分[x(CH4)=0,0.5,1]的无侧限贫燃预混氨-甲烷-空气火焰研究,当进气流速大于5m/s时,氨-空气混合气无法被点燃,而添加50%甲烷后,层流火焰速度较当量比φ=0.8的氨-空气火焰提高了2倍,且火焰更加稳定。Ariemma等考察了不同氨/甲烷比下燃料气的燃烧特性,发现相比纯氨,混合燃气在工作温度与等效比方面具有更高的稳定运行范围,但NOx排放量也相应增加,并强烈依赖于φ值。如图2所示,Filipe等利用现有的燃气轮机对氨-甲烷混合气燃烧产物进行了分析,发现在相同条件下,只使用氨时产生的NOx最少,但残余氨体积分数超过1500×10-6,当适当掺入甲烷后,尽管会使尾气中NOx排放量有所增加,但残余氨的体积分数可大幅降低到30×10-6以下。
3.3工业氨燃烧技术
自从氢能的工业化发展到达瓶颈以来,世界各国开始对氨燃料的规模应用进行开发。日本AIST公司与东北大学正进行50kW级微型燃气轮机的氨直燃试验,目前已实现了氨的完全转化以及尾气中NOx的抑制。丰田等公司利用300kW级小型燃气轮机成功完成了100%氨稳定燃烧试验。IHI与东北大学等机构在2000kW级燃气轮机中完成了氨/甲烷混燃比例从20%到70%的过渡试验,并计划下一步开发100%氨专烧技术。近期,国家能源集团在氨掺煤领域开展了40MW级燃煤锅炉掺氨35%的中试,氨燃尽率达99.99%,实现了煤电行业的技术突破,也证明氨具有替代煤粉燃烧发电的潜力。
4 氨燃料电池
相较于裂解制氢与直接燃烧,燃料电池的优势是可以更大限度地利用氨分子中的化学能,整体效率较高。氨燃料电池可以根据不同的类型进行分类,如表1所示。
4.1质子交换膜燃料电池(PEMFC)
PEMFC是一种通过氧化还原反应将化学能转化为电能的装置,具有高效率、高功率密度和环保等多项优点,并在过去20多年里取得了长足进步。目前对PEMFC的研究大多集中在氢能领域,但其对氢气的纯度有严格的要求。研究表明,PEMFC阳极进料中的痕量NH3会导致相当大的性能损失,主要原因是NH4+离子置换H+导致Nafion®膜电导率降低,且NH3的存在会使得膜发生不可逆的降解。2019年,国际标准化组织针对PEMFC提出了低至0.1×10-6的NH3体积分数阀值,因此,当氨被用作PEMFC的燃料源时,通常需要先分解,然后进行分离和纯化,以除去未转化的氨和氮,未转化的氨可以被酸性沸石和树脂有效吸收,而氮气与氢气的分离膜则采用膜分离技术。Cha等制造了由氨裂解器、吸附塔和聚合物电解质膜燃料电池组成的千瓦级发电系统,该发电系统可成功使无人机飞行2h。尽管分离和纯化过程不可避免地会产生大量成本,但氨燃料PEMFC仍具有吸引力。
4.2碱性燃料电池(AFC)
AFC是第一种投入实际应用且能够提供强大动力的燃料电池,具有非常高的电气效率,可以内置到分布式发电厂中,这些优势使得AFC系统的开发逐渐成为热点话题。2008年,Ganley以KOH-NaOH低共熔混合物作为电解质,在200~450℃工作温度下进行了氨燃料电池的性能测试,450℃时能产生大约40mW/cm2的功率。不同工作温度下的极化特性表明,该燃料电池性能受到欧姆电势损失的影响。为了解决电池的耐久性问题,Lan等对AFC损耗机理进行了深入研究,发现空气中的CO2与氢氧化物电解质反应后会形成碳酸盐沉淀,造成电池中毒,而在新的碱性膜燃料电池(AMFCs)系统中,虽然碱性膜仍能与CO2反应生成CO32-,导致OH-的电导率降低,但不会形成沉淀,避免了传统AFC易中毒的问题。
4.3固体氧化物燃料电池(SOFC)
SOFC因燃料灵活性和高效率而成为燃料发电的理想选择之一。单独应用SOFC时热效率最大在50%左右,目前大多技术都是将SOFC与底部热循环相结合(如图3所示),此方式的能量利用率高,总效率可超过70%。近几年SOFC阳极电催化剂的开发主要集中在Ni上,在超过600℃的高温下具有极高的氨转化率,并且对NO的选择性非常低[29]。Stoeckl等[30]评估了Ni-YSZ阳极上不同温度下的氨转化率,发现温度从700℃提高到800℃,氨转化率增加到近100%,此时的性能与氢燃料电池相似。这表明在未来氨将有可能替代氢气,成为最重要的新型能源之一。
5、结语与展望
在氢能技术发展到瓶颈期后,许多国内外企业已开始布局氨能源。我国拥有全球最大的合成氨市场,成熟的储运技术使得氨作为储氢材料或新型燃料都有着广阔的应用前景。在氢能领域,氨是理想的氢载体之一,将有希望实现低温高效的氨裂解制氢,且可能会逐步呈现出氨氢融合的趋势。氨直烧方面,由于纯氨难以实现稳定燃烧,结合我国的能源现状,可选择“分步走”的混烧战略,再通过碳捕集技术将尾气中的CO2进行回收利用,形成相对封闭的碳循环过程。固体氧化物燃料电池作为后起之秀,拥有分布式发电、氨动力汽车等广泛的应用场景,且对氨表现出极高的耐受性,未来可能会成为新型能源的重要组成部分和实现碳中和的重要途径。
绿氢制取路径及成本分析
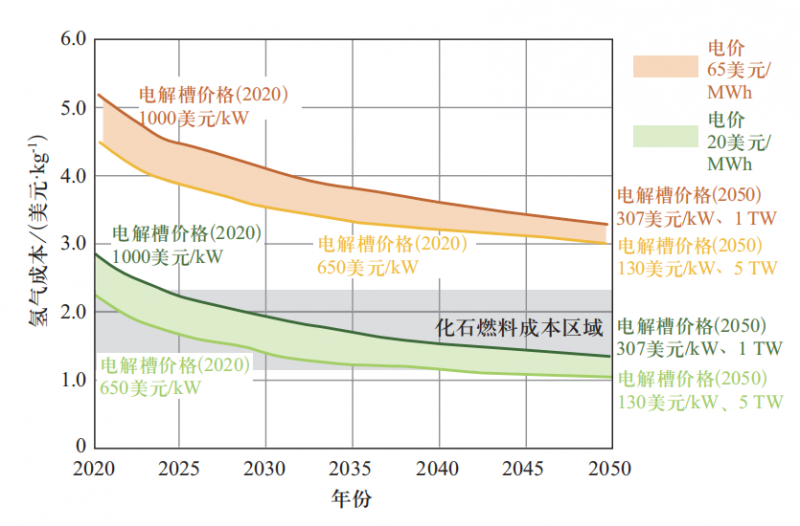
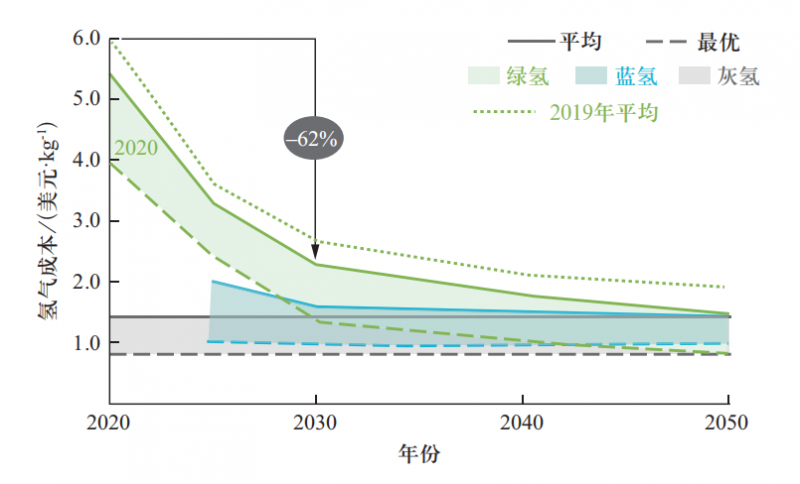
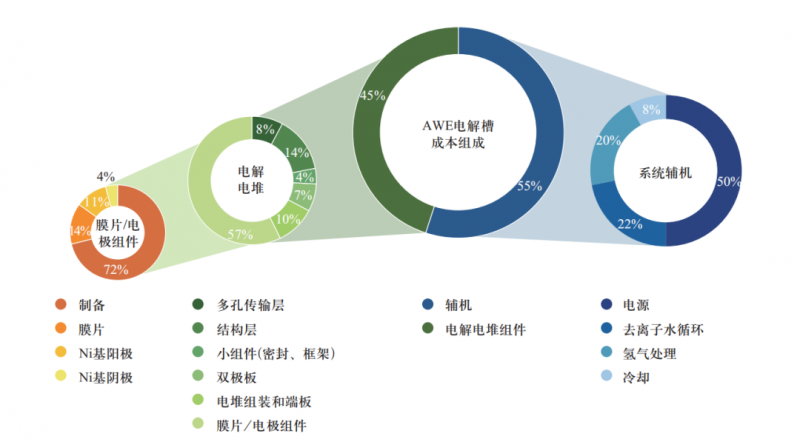
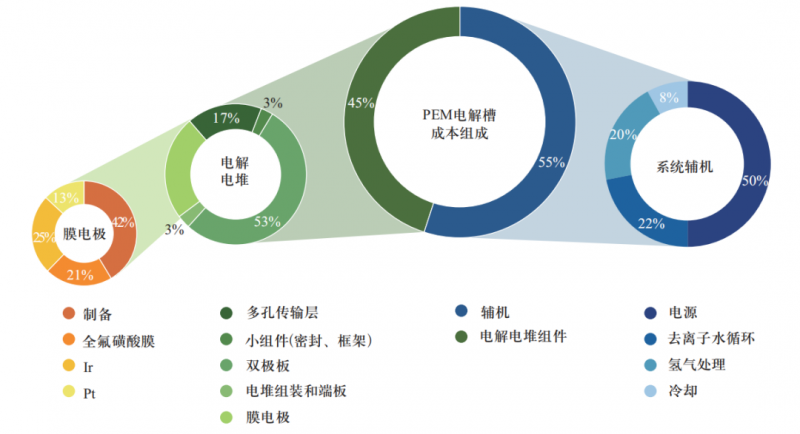
1. 绿氢的制备来源于可再生能源生产的电力,以清洁、用途广泛为显著特点,助力难以脱碳行业的实现去碳化,预计到2050年将占全球一次能源供应的15%。
2. 根据我们的模型预测,2020年绿氢成本每公斤4.2美元,2030年为1.9美元,2050年为1美元。分区域的绿氢价格介于0.8美元到1.3美元之间,中东/北非价格最低,欧洲价格最高。
3. 市场潜力大、成本低的地区将引领第一波绿氢发展热潮,领跑者很可能是欧洲、中东/北非及澳大利亚。
4. 美国和中国将通过绿氢蓝氢同步发展迎头赶上,实现氢能自给自足。中东/北非、澳大利亚及西拉美将成为氢能出口枢纽。欧洲依然主要发展绿氢,叠加进口来满足氢能需求。
5. 2020年生产绿氢的电力成本平均为44美元/兆瓦时,占到总成本的56%,平准化度电成本在近几年将大幅下降,之后趋于平稳。2050年电力成本预计为17美元/兆瓦时,占到生产绿氢总成本的70%,因此电力成本差异将直接导致绿氢成本存在地区性差异。
6. 到2050年,电力成本、电解槽投资成本的加和将占到削减了的总成本的一半,另外随转换效率和负载因数持续优化,贡献可达削减了的总成本的17%。
7. 在欧洲,到2030年绿氢的盈亏平衡点有望与灰氢、蓝氢持平,到2040年有望与LNG、天然气持平。
8. 在氢能消费端,2020年绿氢将开始在供热和重卡行业得以应用,到2030年很可能作为极具价格竞争力的能源在主流工业领域和交通领域推广应用。
平台声明:该文观点仅代表作者本人,氢能网系信息发布平台,我们仅提供信息存储空间服务。
发表评论 取消回复